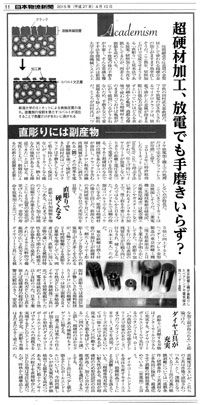
It seems a process of Tungsten Carbide which is often used for cold forging and cold heading will become further effective.
In those years 『Direct Carving 』which is completed only by machining and traditional processing of EDM (Electric Discharge Machining) with grinding are competing hard each other.
Both technology increased the value.
Professor of Niigata University, faculty of engineering Mr. Takeo Tamura has developed a upsetting common sense technology of No need of hand lapping after wire EDM.
Micro crack is a weak point of wire EDM. It is a surface fine crack always happen by tensile stress when EDM melted metal sets.
Tungsten Carbide is usually used at harsh circumstances.
If this micro crack is not taken care, crack expands and causes a damage.
The surface portion is normally eliminated by hand lapping.
But Mr. Tamura says complete crack less process is possible only by wire EDM.
SI cut (Surface Integrity cut) process which is registered patented on 2012 is the one which keeps limit distance that wire and work does not discharge and operate only by electric field.
Then Cobalt which has a function of paste in Tungsten carbide melts out and 1 micron thickness of melted resolidification layer can be pealed off clearly.
Mr. Tamura verificated an effect by using electron microscope 『Micro crack cannot be totally eliminated by hand lapping, but SI cut can do it perfectly. We can confirm a strength of original metal.』Certainty and no need of any additional machine tool are good points too.
It seems SI cut will be widely used in industry.
Mitsubishi Electric, advanced technology laboratory in Amagasaki, started studying its possibility it can be used for inconel process to eliminate latter process in aviation engine and gas turbine production.
In case of Inconel, paste function can be done not by cobalt but by nickel, principle is the same as Tungsten Carbide.
They’ll start co-study in July and try to make use of it in 3 years.
Direct carving makes it harder.
Direct carving is increasing its additional value.
So far its merits are shortening the process time and stabilization of quality as no hand work is required.
But Tokyo Byora Koki Co., Ltd. Manufacturer of header dies in Saitama Niiza and Nihon Institute of Technology (NIT) announced direct carving processed dies lifespan becomes 1.5 times in comparison with traditional EDM.
The dies processed by direct carving becomes harder because a residual stress on surface is added on compression direction, told NIT.
Tokyo Byora Koki is operating more than 90 percent with Tunsten Carbide, and traditional EDM process of narrow hole -> wire-> engraving-> lapping occupies majority but direct carving process is increasing by using 3 axis machining center, 24 hours operation.
Both organization has announced about characteristic of working material by difference of knife used for direct carving at “Precision industry society in spring convention”.
They said comparatively wide working range of two blade radius diamond coating tools process the work material (Tungsten Carbide VU-70, material particle diameter more than 5 micron which is considered high level process is difficult with direct carving) used to be process face roughness 4 times more in comparison with 6 blades PCD (polycrystalline diamond sintered
body ) but more than 1.5 times better in comparison with electroplated grinding wheel.
NIT told as a conclusion “ By using 6 blades PCD tools, particle diameter’s influence to Tungsten Carbide is comparatively small so stable surface can be obtained.”