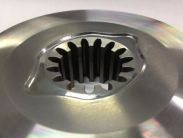
Our company is established in 1961. We are mainly manufactured the cold heading die, the cold forging die and the press die made from the special metal such as Tungsten Carbide and the component of press die.
We were focused on a possibility that the special metal such as Tungsten Carbide from early stage, the electric discharge machine was equipped, and it is worked out as the die material. The small diameter hole to a hard metal, a variant, deep hole processing, and mirror surface (lapping) processing technology have been maintained. The Die for the screw as the smallest in the world (hole diameter:0.24mm) is a proof of the technology.
Therefore, we have full knowledge of the limit for electrical discharge machining technology. Its productivity is not good, in order that electrical discharge machining may prepare the electrode beforehand and may fabricate it by electric discharge energy. We would like to develop in the future, the day or the new process of when.
Although long years were required, we have succeeded in mass-production of the die by direct cutting to Tungsten Carbide without Lapping process. Now the time, mass-productions are maintaining at 200~500pcs./month for the small diameter of electric contact and the rivet.
Research is maintained in order to extend also after that the die/mold which can be mass-produced, and we have succeeded the mass-production of curved surface shape and the big diameter size lately, and also came up to stand a bearing steel ball ds type to the customer requirements.
It is believed that our die/mold technology progresses unless a pace is stopped itself. Also it is a subject that the engineering development about material.
Therefore, we decided to name our original Tungsten Carbide die 「Tokyo-ACE I (the first generation). 」
The feature of Tokyo-ACE I (the first generation)
- Ultra long lifetime 1.5 times more than present product
- Quick Delivery 1/5 times of present product
- Low cost 10-20% less than present product
- High accuracy Stable with micron(μ) accuracy
The production method of Tokyo-ACE
- Make Specular Surface to Direct Cutting Fabrication by Machining Center.
- Surface by mirror quality in Machining Center without Lapping Processing.
- Carry out 24 hours for die production without man operation of Machining Center.
About the diamond tool for Tungsten Carbide processing
A whetstone with an axis, a DIA coating cutting tool, a sintered-diamond (PCD) tool, a single sintered-diamond tool, etc. are among the diamond tools into which difficult curving material is processed. The proper use which was set to cut Tungsten Carbide and was united with work form, the purpose, and the use is required.
In our company, when carrying out direct engraving of the metallic mold made from Tungsten Carbide of about ±0.005 dimensional tolerance, fundamentally, the whetstone with an axis is carrying out proper use which calls rough picking processing and a DIA coating cutting tool inside finish-machining, and calls a sintered-diamond tool finish-machining.
The reason is because it judged that the whetstone with an axis was finished from maintenance of a tool size, and it was a little hard to treat it as a tool of managing.The DIA coating cutting tool thinks that it is difficult as a finishing tool from the tool life of what can obtain the field coarseness near a mirror surface according to processing conditions, the unevenness on quality condition to coating, etc. In that respect, since it can be comparatively handled stably in dimensional control and mirror surface quality, the sintered-diamond tool has been positioned as a finishing tool.